Iot Remote Asset Monitoring Solution Management and Monitoring with IoT
Iot Remote Asset Monitoring Solution Management and Monitoring with IoT
Blog Article
Iot Global Top 10 Monitoring Tools for IoT
The industrial panorama is undergoing a profound transformation, thanks to the arrival of IoT connectivity solutions for manufacturing automation. These options not only enhance operational effectivity but in addition allow manufacturers to leverage knowledge in real-time, making knowledgeable decisions that enhance productivity.
Manufacturing processes are getting more advanced, and the need for streamlined operations has never been larger. IoT connectivity solutions facilitate seamless communication between machines, sensors, and operators on the manufacturing unit floor. This interconnectedness results in improved monitoring and management, decreasing downtime and minimizing the possibilities of operational bottlenecks.
Iot Remote Asset Monitoring Solution How IoT Remote Monitoring Functions
Real-time data assortment is probably certainly one of the standout features of IoT in manufacturing. Through smart sensors, machines can ship and receive data instantaneously. By using real-time analytics, producers can assess tools health and performance, resulting in predictive maintenance. This proactive strategy prevents surprising failures that can disrupt the manufacturing line.
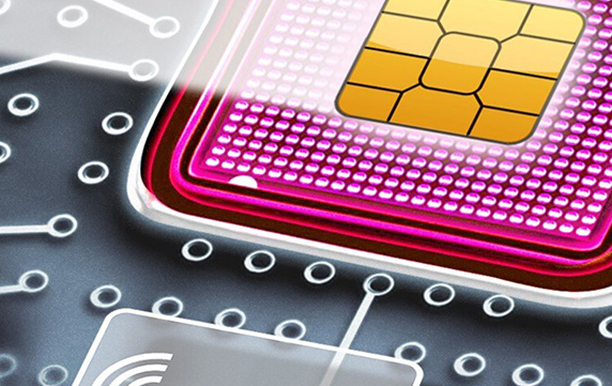
The integration of IoT technologies introduces a degree of flexibility that conventional manufacturing might solely dream of. With the potential to remotely monitor and control processes, manufacturers can regulate operations based on demand fluctuations. This agility not only boosts productivity but also allows for customized manufacturing options tailor-made to particular shopper needs.
However, the adoption of IoT connectivity solutions is not with out challenges. Cybersecurity turns into a significant concern as extra units hook up with the internet. Ensuring the integrity of sensitive manufacturing information is of utmost significance. Manufacturers must put money into sturdy safety measures, together with encryption and regular audits, to safeguard their systems against potential threats.
Implementing IoT options additionally requires a cultural shift within organizations. Employees must be skilled to know and harness the potential of these new technologies. This can foster a collaborative environment where human experience combines with machine effectivity, ultimately leading to larger innovation and progress.
Remote Monitoring Using Iot Stand-Alone Remote Monitoring Devices

Data plays a pivotal function in the success of IoT initiatives. With countless information factors generated by interconnected units, producers are sitting on a gold mine of data. Analyzing this knowledge can uncover insights that drive improvements in processes, high quality management, and provide chain administration.
Supply chain optimization is another space where IoT options shine. By monitoring materials and merchandise all through the availability chain, manufacturers can higher anticipate delays and manage stock. This visibility ensures that the proper materials arrive at the right time, minimizing waste and improving general effectivity.
It Remote Monitoring Software Protecting IoT Devices through Monitoring
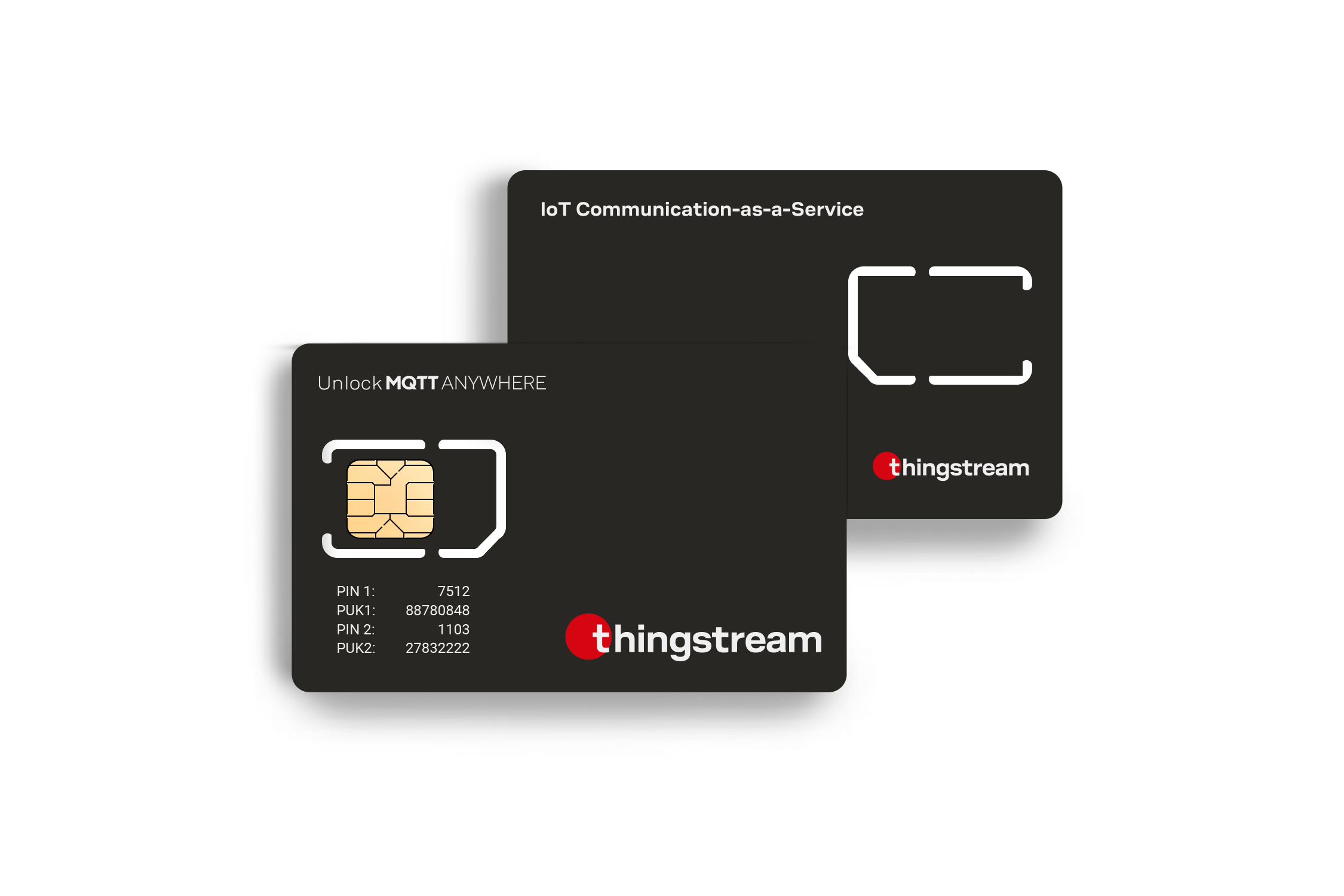
Collaboration amongst varied stakeholders becomes less complicated with the implementation of IoT connectivity options. Different departments within a company can entry real-time data, permitting for more knowledgeable decision-making. Furthermore, companions and suppliers can hyperlink their methods with manufacturers, streamlining processes and enhancing coordination across the board.
The scalability of IoT solutions is a big benefit for producers. As businesses develop, their wants evolve. IoT systems may be tailored and expanded to satisfy these altering requirements. This adaptability ensures that manufacturers remain competitive in a quickly evolving market.
In terms of energy efficiency, IoT connectivity solutions can result in substantial financial savings. Smart energy management techniques can monitor energy consumption patterns and adjust accordingly. This not solely reduces operational prices but also positively impacts the environment by lowering carbon footprints.
As manufacturers embrace the digital era, the utilization of IoT connectivity options might be imperative for staying forward of the competitors. The potential for innovation is immense, with opportunities to boost product high quality, speed up production cycles, and create entirely new business models. Remote Monitoring.
Remote Monitoring Solutions for Remote Asset Monitoring
Virtual and augmented actuality may also be integrated into IoT frameworks for coaching functions and operational administration. With real-time data superimposed onto bodily environments, employees get enriched coaching experiences, reducing the time taken to turn out to be proficient in new methods.
The future of producing might be defined by those that can harness the facility of IoT. With the proper strategies in place, producers can additional resources navigate the complexities of the digital panorama, turning challenges into opportunities. As know-how continues to advance, the mixing of IoT connectivity options won't solely rework the way products are made but additionally redefine the entire supply chain ecosystem.
While many producers have begun their journey into IoT, people who remain hesitant should acknowledge the need for transformation. Investing in IoT solutions today can pave the best way for a extra resilient and efficient manufacturing environment. As the industry turns into more and more competitive, early adopters of IoT technologies will probably acquire the upper hand.
Iot Remote Monitoring Solution Custom Solutions for Asset Monitoring
In an era where agility and adaptability are essential, IoT connectivity options for manufacturing automation stand out as catalysts for change. By embracing these technologies, producers not only enhance their operational capabilities but additionally prepare themselves for a future filled with immense possibilities.
The synergy between human intelligence and machine learning pushed by IoT will lead to smarter factories. Manufacturers is not going to only meet current market demands but in addition anticipate future trends, fostering continuous enchancment and innovation. This holistic method ensures that the manufacturing sector thrives even in the face of worldwide challenges.
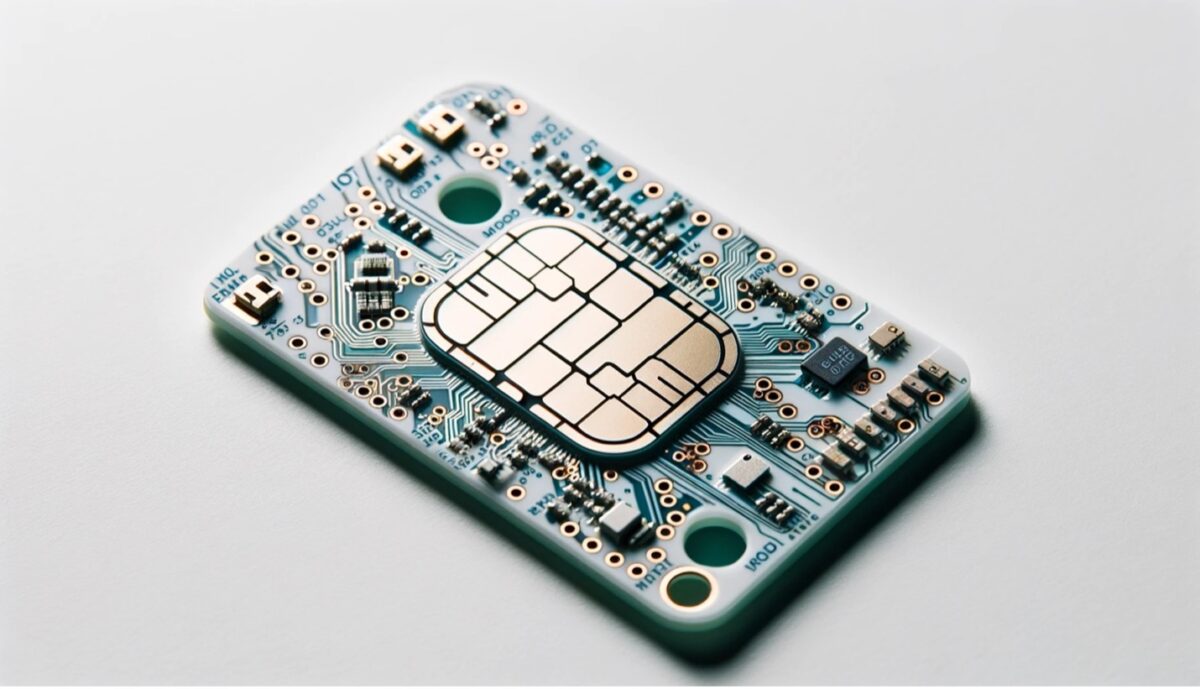
In conclusion, the integration of IoT connectivity options for manufacturing automation marks a big shift in how industries function. As these technologies evolve, their impression on productivity, efficiency, and sustainability will solely develop stronger. Manufacturers who select to have interaction with these advancements will doubtless discover themselves on the forefront of the business, reaping the advantages of a more related and intelligent manufacturing ecosystem.
- Enhances real-time data collection from machines, allowing for quick adjustments to operations and lowering downtime.
- Supports remote monitoring and predictive maintenance, enabling producers to predict tools failures earlier than they happen.
- Facilitates seamless integration of legacy methods with modern IoT units for enhanced operational efficiency.
- Improves supply chain management by way of better visibility and tracking of inventory levels and production timelines.
- Enables data-driven decision-making by consolidating insights from varied units into a single analytics platform.
- Reduces energy consumption by optimizing machine utilization and implementing smart energy administration methods.
- Empowers workforce collaboration through connected wearables that provide immediate entry to critical data on the factory flooring.
- Supports enhanced safety protocols by using IoT sensors to watch hazardous situations and alert personnel in real-time.
- Leverages cloud computing to retailer and analyze large volumes of knowledge, selling scalability and suppleness in manufacturing operations.
- Encourages continuous improvement via automated suggestions loops that identify inefficiencies and suggest optimizations.
What are IoT connectivity solutions in the context of producing automation?undefinedIoT connectivity solutions for manufacturing automation discuss with the technologies and networks that allow gadgets and machines to speak and exchange data over the internet. These solutions improve operational efficiency, monitor asset performance, and facilitate real-time knowledge analytics.
Remote Monitoring Using Iot Guide to Real-Time IoT Monitoring
How do IoT connectivity options improve manufacturing efficiency?undefinedBy connecting gear and systems, IoT connectivity options enable real-time monitoring, predictive maintenance, and automatic processes. This results in reduced downtime, optimized useful resource usage, and ultimately larger production effectivity.
What kinds of IoT connectivity options are available for manufacturing?undefinedCommon IoT connectivity options embody cellular networks (4G/5G), Wi-Fi, LPWAN go to my blog (Low Power Wide Area Network), and Ethernet. The choice depends on elements like range, information necessities, and the environment in which the units function.
Can IoT connectivity solutions enhance security in manufacturing?undefinedYes, IoT solutions can improve safety by monitoring tools health and worker circumstances. Real-time alerts can notify personnel of potential hazards, permitting for timely interventions and decreasing office incidents (Role Of Smart Sensors In Iot).
What position does information analytics play in IoT connectivity for manufacturing?undefinedData analytics is integral because it transforms the vast amounts of knowledge generated by IoT gadgets into actionable insights. This helps in decision-making processes, optimizing operations, and implementing continuous enhancements.
Remote Monitoring Solutions Management of IoT Remote Monitoring
How safe are IoT connectivity options in manufacturing?undefinedSecurity is a important concern; many IoT connectivity options make use of encryption, authentication, and community segmentation to guard knowledge. Regular software program updates and monitoring also help safeguard against potential vulnerabilities.
What are the key challenges in implementing IoT connectivity in manufacturing?undefinedChallenges include integrating with existing systems, guaranteeing information safety, managing system compatibility, and scaling the solution successfully. Addressing these challenges typically requires a strategic strategy and collaboration with technology partners.
Iot Global Critical Remote Monitoring and Maintenance
How can small manufacturers profit from IoT connectivity solutions?undefinedSmall producers can acquire important advantages, such as improved efficiency, reduced operational costs, and better decision-making capabilities. With reasonably priced IoT options, they'll optimize useful resource use and compete extra successfully in the market.
What is the cost of implementing IoT connectivity solutions in manufacturing?undefinedThe cost varies based on the scale of implementation, the technology chosen, and the specific needs of the facility. While preliminary funding can be substantial, the long-term financial savings and productiveness features usually outweigh the prices.
Report this page